When it comes to creating outdoor stickers that last, not all printing methods, inks, or materials are created equal. As experts in sticker manufacturing, we’ve seen it all—stickers that fade in a few months, adhesives that peel in the rain, and promises from printers that don’t quite hold up in real-world conditions.
But here’s the good news: achieving long-lasting, weather-resistant stickers isn’t rocket science. It’s all about understanding the right combination of print processes, ink types, and materials. In this guide, we’ll dive deep into the secrets of outdoor sticker durability and help you make informed decisions for your next project.
Why Outdoor Durability Matters
Imagine this: you’ve just spent time and money designing a killer sticker for your brand. You stick it on a car window or a piece of outdoor equipment, expecting it to turn heads for years. Fast forward three months and the vibrant colors are now a dull, faded version of themselves.
Durable stickers aren’t just about looking good—they’re about building trust with your audience. A faded or peeling sticker can send the wrong message about your brand. That’s why it’s crucial to get it right from the start.
Let’s Talk Printing Processes
The foundation of any durable outdoor sticker starts with the printing method. Here’s a breakdown of the most common options:
1. Screen Printing: The Heavyweight Champion
Screen printing is the gold standard for outdoor durability. Why? What makes screen printing so special? It uses thick, UV-stable inks that stand up to the elements like a champ. Whether it’s rain, sun, or snow, screen-printed stickers hold their color and integrity for years.
Best for: Marketing and promotional stickers, heavy-duty equipment, and long-term outdoor use.
2. Outdoor Digital Printing: Versatile and Modern
Digital printing has come a long way in recent years. High-quality outdoor digital printers use UV-cured inks that are resistant to fading and can last 3+ years outdoors without additional lamination.
Best for: Complex designs, gradients, and smaller quantities where screen printing might not be practical.
3. Flexographic (Flexo) Printing: Great for Volume, Not for the Outdoors
Flexo printing is often used for high-volume label production, but here’s the catch: standard flexo inks aren’t designed for outdoor use. They can fade in as little as three months. Even with “extended-life” inks, you’re looking at 9-12 months at best, which might not cut it for most outdoor applications.
Best for: Indoor labels, temporary stickers, or applications with limited sun exposure.
4. Short-Term Digital Printing: High-Quality, But Limited Longevity
Short-term digital presses like HP Indigo and Xeikon (toner-based presses) are commonly used for printing small to medium quantities of custom stickers. These presses offer excellent color reproduction, crisp details, and fast turnaround times, making them a favorite for indoor and temporary applications.
However, when it comes to outdoor durability, these stickers fall short. While they might look great fresh off the press, exposure to sunlight and the elements quickly takes its toll. Without added protection (like lamination), stickers printed on these presses are prone to fading, sometimes within a matter of weeks.
Best for: Indoor applications, product packaging, and short-term promotions.
5. Offset Printing: High-Volume, But Not Outdoor-Friendly
Offset printing is another popular method for large sticker runs. Known for its precision and cost-effectiveness at scale, offset produces vibrant colors and clean details. However, standard offset inks aren’t formulated for outdoor durability. Even with UV coatings, stickers printed via offset struggle to hold up against prolonged sun and weather exposure.
Best for: Business cards, brochures and flyers, magazines and catalogs, packaging, and stationery.
Choosing the Right Ink: It’s More Important Than You Think
The type of ink you use is just as critical as the printing process. Here’s the lowdown:
Solvent-Based Inks: Built to Last
Solvent-based inks are highly resistant to UV rays and water, making them ideal for outdoor applications. These inks chemically bond to the surface, ensuring vibrant, long-lasting colors.
Pros: Extremely durable and weather-resistant.
Cons: They emit VOCs during printing, which requires proper ventilation.
UV-Curable Inks: Modern and Mighty
These inks are cured instantly using ultraviolet light, creating a tough, scratch-resistant surface. They’re perfect for digital printing and offer excellent outdoor performance.
Pros: Environmentally friendly and durable.
Cons: Requires specialized equipment.
Eco-Solvent Inks: Good, But Needs Help
Eco-solvent inks are more environmentally friendly, but they don’t have the same durability as solvent-based or UV inks. Adding a laminate can help extend their lifespan outdoors.
Pros: Lower environmental impact.
Cons: Needs extra protection for outdoor use.
Toner-Based Inks: Vibrant, But Not Built for the Outdoors
Toner-based inks, commonly used in dry toner presses like Xeikon, are made from fine powder fused onto the material using heat and pressure. While these inks produce vibrant colors and are suitable for indoor use or short-term applications, they struggle with outdoor durability. Exposure to sunlight and moisture often leads to fading and peeling, even with protective coatings.
Pros: High-quality color reproduction and fast production.
Cons: Limited resistance to UV exposure and weather conditions.
Decoding the Blue Wool Scale: What It Really Means for Outdoor Stickers
When discussing ink durability, especially for outdoor stickers, the Blue Wool Scale often comes up. This widely recognized scale measures an ink’s lightfastness—or how well it resists fading under light exposure. The scale ranges from 1 to 8, with 1 being the least resistant and 8 offering the highest resistance to UV light.
At first glance, an ink rated 6-8 on the Blue Wool Scale seems perfect for outdoor use. But here’s the catch: it’s not just the rating that matters—ink deposit thickness plays a crucial role too.
Why Ink Thickness Matters
The Blue Wool Scale measures how pigments perform under controlled light exposure, but outdoor environments are anything but controlled. When ink is applied in a thin layer—common with certain printing methods like offset or toner-based processes—the lower pigment density can make the ink more vulnerable to UV rays, even if it has a high lightfastness rating.
Thicker ink layers, as achieved through processes like screen printing or heavy-duty digital printing, offer more protection. The higher concentration of pigments in these thicker deposits creates a barrier against UV degradation, significantly boosting longevity.
Real-World Implications for Outdoor Stickers
It’s important to remember that while the Blue Wool Scale provides a helpful baseline for evaluating inks, it doesn’t account for all the environmental factors stickers face outdoors. Humidity, temperature changes, and pollutants can also take a toll on inks, regardless of their rating.
For customers relying on long-term outdoor performance, pairing a high Blue Wool Scale rating with the right printing process and ink application thickness is essential. And if you want to go the extra mile, consider protective laminates or UV coatings to further extend the lifespan of your stickers.
By understanding the nuances of the Blue Wool Scale, you can make smarter choices about your sticker’s design, materials, and printing process to ensure they not only look great but last as long as you need them to.
Materials Matter: Pick the Right Substrate
The material your sticker is printed on plays a huge role in how well it performs outdoors. Check out our complete guide on sticker materials to learn more.
Vinyl: The MVP of Outdoor Stickers
Vinyl is the go-to material for outdoor stickers. It’s durable, waterproof, and adheres well to a variety of surfaces.
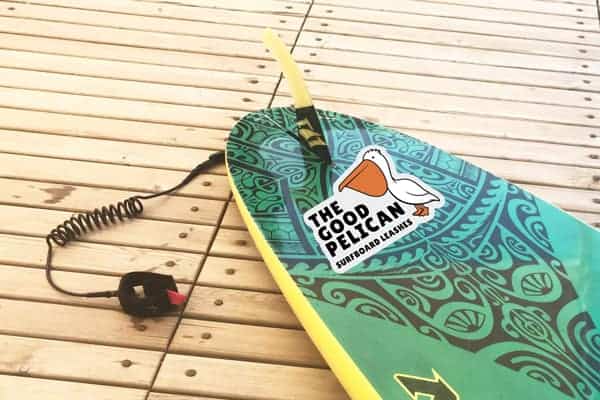
Polyester (PET): High-Performance Durability
Polyester is incredibly resistant to UV exposure and temperature changes, making it a great choice for harsh environments. This material is often used for equipment stickers such as HVAC reminder stickers or industrial labels.
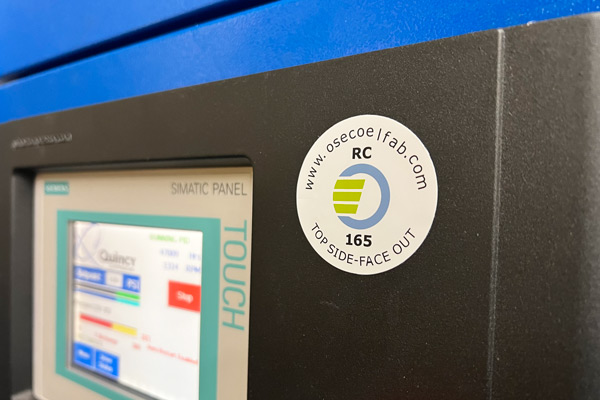
BOPP (Biaxially Oriented Polypropylene): Perfect for Product Labels
BOPP is a lightweight, flexible, and moisture-resistant material, making it an ideal choice for product labels and indoor applications. It’s available in clear, white, and metallic finishes, providing plenty of creative options for packaging. However, BOPP isn’t designed for long-term outdoor use. Without UV protection or additional coatings, it can fade and degrade quickly when exposed to the elements.
Best for: Product labels, cosmetic packaging, and indoor applications.
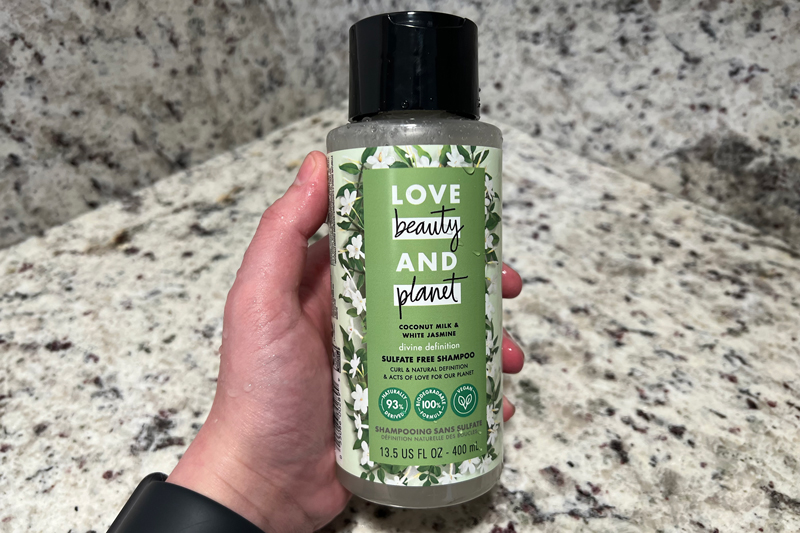
The Case for Laminates: Are They Worth It?
Laminates are often seen as a quick fix for extending sticker durability, especially when it comes to outdoor exposure. They serve as an extra layer of protection, offering resistance to UV rays, moisture, and abrasion. For prints like eco-solvent prints or stickers exposed to constant wear—such as those on tools, equipment, or vehicles—adding a laminate is almost a necessity.
However, it’s important to understand that laminates don’t solve everything. They work as a shield, enhancing the performance of high-quality inks and materials. If your sticker’s ink or material isn’t up to the task, no amount of lamination will fully protect it from fading, peeling, or cracking. Laminates are best viewed as a complement to a solid foundation, not a cure-all.
Laminates and Aesthetic Appeal
Beyond protection, laminates offer a key benefit—they can change the look of your stickers. For screen printed or long-term outdoor digital prints, the decision to add a laminate is often more about the visual appeal than the protective benefits.
- Gloss Laminate: Adds a shiny, reflective finish, making colors pop and providing a sleek, professional look. This is a great choice if you want to make your sticker stand out in both appearance and durability.
- Matte Laminate: Offers a more understated, sophisticated finish that reduces glare and can give your stickers a more subtle, premium feel. This is often chosen for its aesthetic rather than its practical purpose, as it provides protection but doesn’t enhance the sticker’s durability as much as gloss laminates in high-abrasion scenarios.
In the end, whether you choose gloss, matte, or another finish, laminates offer a unique opportunity to both protect and personalize your stickers. They help preserve the integrity of your design while letting you fine-tune the overall aesthetic, ensuring your brand stands out—inside and out.
Pro Tips for Maximum Outdoor Durability
- Know Your Environment: Stickers in sunny climates need more UV protection than those in shaded areas.
- Test, Test, Test: Before ordering a large batch, request samples and test them in real-world conditions.
- Work with Experts: A knowledgeable printer can guide you toward the best combination of materials, inks, and processes for your needs.
Why We’re Obsessed with Sticker Quality
At Comgraphx, we don’t just print stickers—we obsess over making them last. With three distinct print processes (screen printing, outdoor digital printing, and flexo printing), we tailor every project to meet your specific needs. Our goal is simple: to ensure your stickers make an impact for as long as possible.
When it comes to outdoor durability, we’ve got the tools, knowledge, and experience to help your brand shine in any environment.
Need help with your next outdoor sticker project? Let’s talk! Whether you’re looking for guidance or a custom quote, we’re here to help your brand stand out—and stay that way.